Companies often stagnate or face declining performance due to outdated processes, inefficiencies, and a lack of adaptability. The absence of a continuous improvement approach can lead to reduced competitiveness, lowered employee morale, and decreased profitability.
Continuous improvement is needed when the company faces the following:
- Deficiencies: Products not meeting set quality standards, leading to scrapping. Results in time consumption for both rectifications and administrative tasks.
- Overproduction: Exceeding the necessary production levels. Results in surplus stock, incurring storage and logistic costs.
- Stagnation: Unnecessary delays in processes or actions.
Untapped Potential: Not leveraging the complete skills and capabilities of employees. This can result in effective collaboration, better communication, and redundant tasks. - Transit: The relocation of goods without adding value. Induces additional expenses without enhancing product worth.
- Stockpile: Accumulation of unsold products.
- Movements: Redundant shifts of workers or machinery that don’t enhance the value.
- Needed Steps: Superfluous procedures or tasks. Involves additional resources, materials, and wear on equipment.
What is Continuous Improvement?
It is the process of making small growth corrections that add up to estimated results based on keen and structured observation of the process carried out in the organization.
Continuous Improvement, also known as Kaizen, is a method for identifying opportunities for streamlining work and reducing under-performance. This practice was formalized through the Lean/Agile/ Kaizen to identify the required learning opportunities for employees.
Did you know?
Researchers say 75% of businesses worldwide have adopted continuous improvement strategy to achieve operational excellence.
The main idea behind continuous improvement is that every department/sector needs to be fixed, and there is much room for improvement. Organizations aim to squeeze out waste, optimize resources, and upskill their professionals to meet the company’s bottom line.
In this blog, we will be discussing the importance, stages, and strategies for continuous improvement.
Importance of Continuous Improvement
As you have glanced through the meaning of continuous improvement, it is best to understand its importance and how it helps with organizational growth.
- Identifies the areas of improvement, can create a more streamlined workflow that cuts down unwanted resources, and advises on managing time.
- As there is continuous improvement among the teams, employees automatically search for growth opportunities within the organization for better communication and reputation.
- Reduces the defects and smoothens the process. This brings happier customers and reduces the influence of rework and replacements.
- If the above importance is kept at hand, a small change might take time but eventually reduces time constraints, so the product and services can be seen on the market faster.
- Constantly helps to stay ahead of the competition and provides opportunities to test new ideas quickly and cheaply to see if they are worth pursuing.
For any business worldwide, adapting to the changes is critical to success.
4 Stages of Continuous Improvement
Continuous improvement is also known as PDCA Cycle, which stands for Plan-Do-Check-Act. This is a practice/culture that encourages all employees to look for ways to enhance business operations.
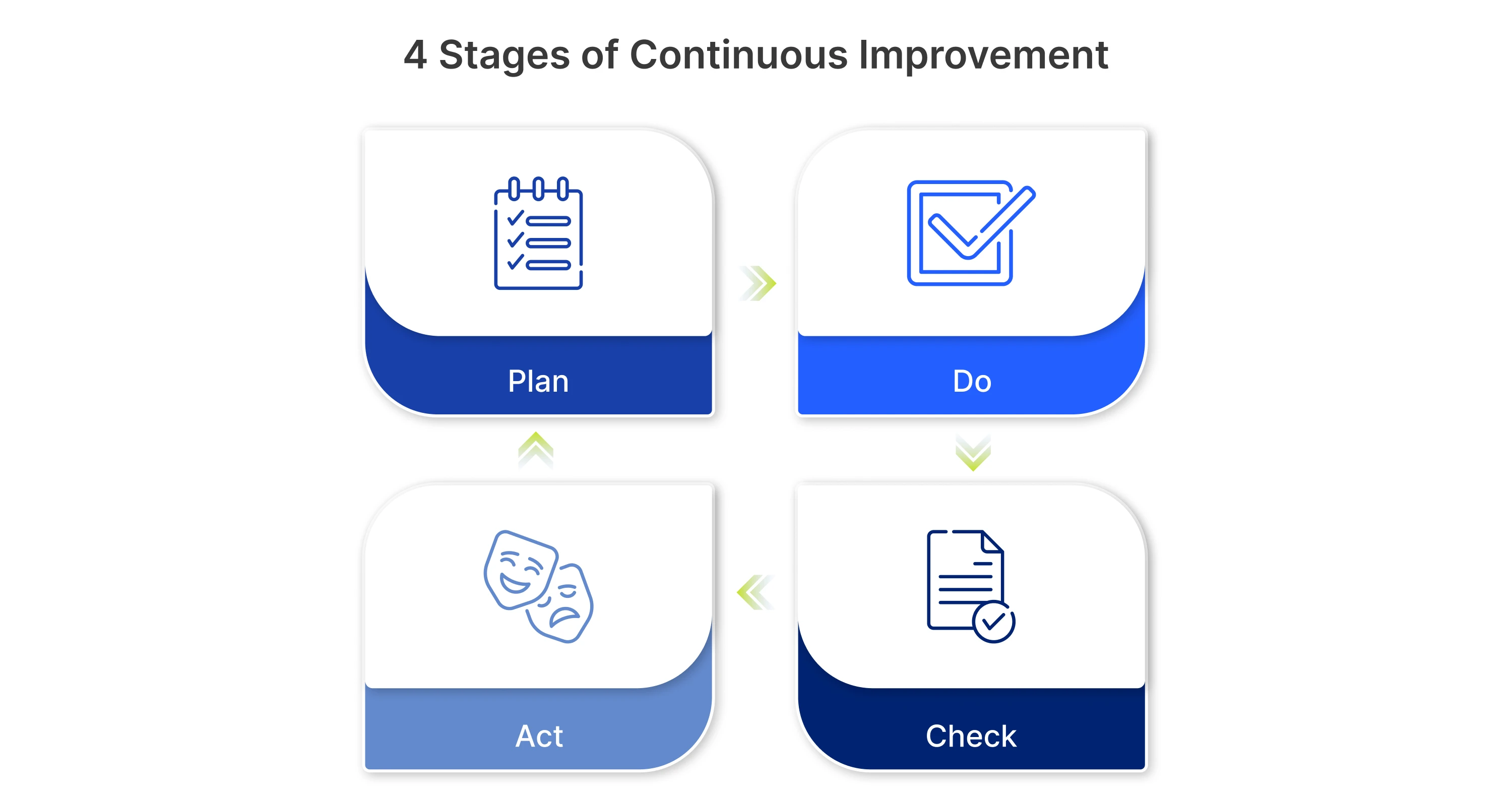
- Plan: Identifying the opportunities and list the action plan for ease of management.
- Do: Once the opportunity is identified and the plan is set, initially try to implement the plan on a small scale. This is done to measure the effectiveness of the strategy.
- Check: Check if this change in the working strategy before applying it organization-wide. If we receive 40% better leads than the other 60%, who were moderately managing to generate leads through Instagram/Facebook. For example, from this, we can conclude that the change is effective.
- Act: A proven and effective solution for a sustained period should be deployed to the entire organization to reap its benefits.
Remember to do this whenever the company needs to catch up to proactively work towards the organization's growth.
5 Strategies for Continuous Improvement
The goal of improving how things work is super important for businesses. They're always looking for ways to do things better, cut unnecessary steps, and provide the best service to their customers. Over time, experts have devised different methods to help businesses improve.
Think of these methods as tools in a toolbox. Some tools, like Lean, focus on being exact and removing waste. Others, like Agile, are about flexibility and adapting quickly to change. These strategies will discuss five, explaining what makes each special, how to use it, and its pros and cons. By the end, you'll better understand which tool might be best for your business's specific needs.
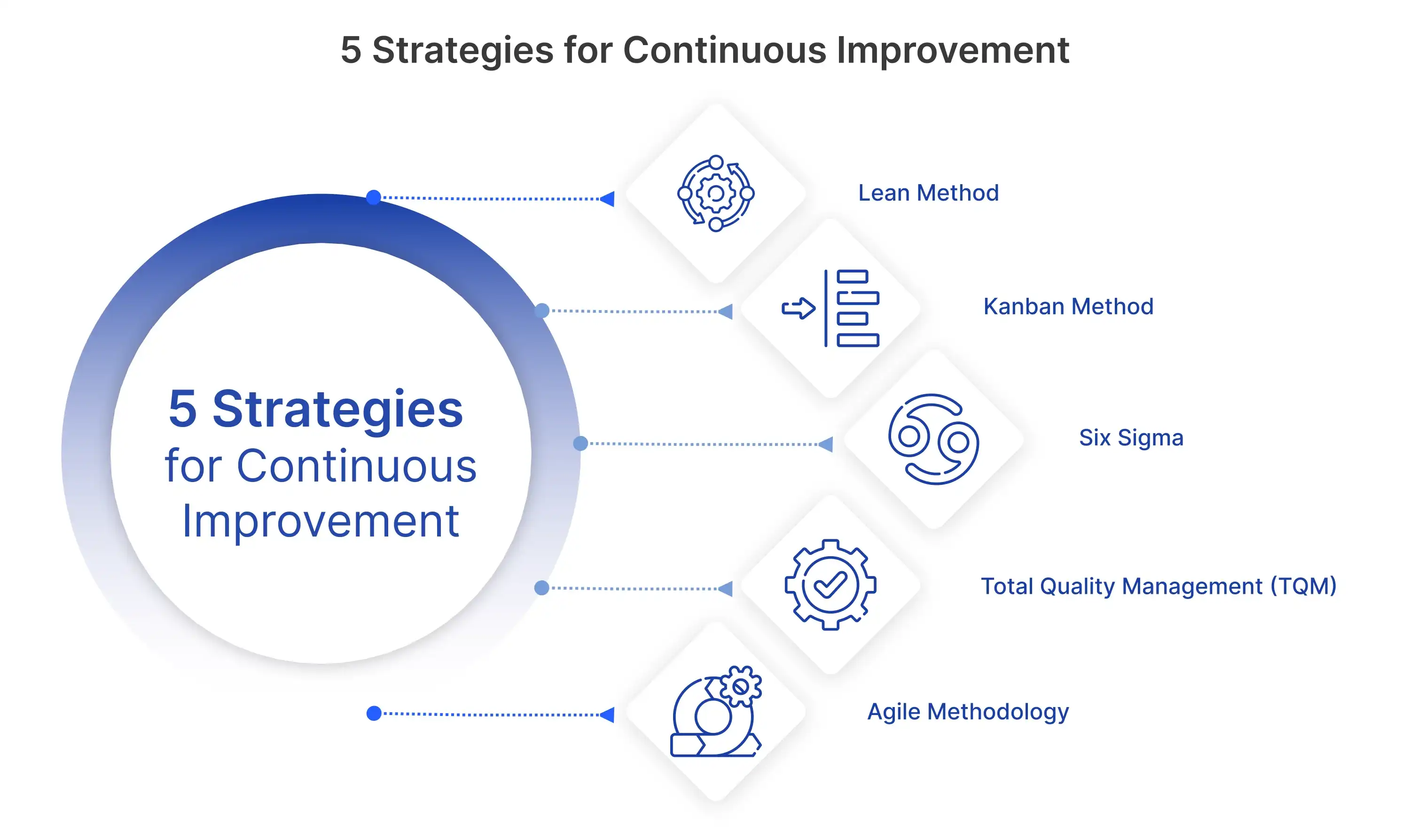
1. Lean Method
How is the Lean Method useful for organizations:
The Lean method focuses on streamlining operations and eliminating waste in processes. For organizations, it offers a structured approach to improve efficiency, reduce costs, and ensure that resources are optimally utilized.
Steps to Follow:
- Value Definition: Identify what adds value from the customer's perspective.
- Value Stream Mapping: Analyze the current process to identify waste.
- Flow Optimization: Ensure a smooth, uninterrupted workflow.
- Pull Production: Produce only what is needed when it's needed.
- Continuous Improvement: Regularly review and refine processes.
Advantages and Disadvantages of the Lean Method:
How the Lean Method strategy is helpful:
The lean method fosters a culture of continuous improvement, helping organizations consistently enhance their operations and deliver higher value to their customers.
Learn More: Lean Corporate training
2. Kanban Method
How is Kanban useful for organizations?
Kanban is a visual tool that helps manage workflow. Organizations can use it to visually track tasks, manage workload, and ensure smoother flow with minimal bottlenecks.
Steps to Follow:
- Visualize the Workflow: Use a Kanban board with columns representing different stages.
- Limit Work in Progress: Restrict the number of tasks in a particular column.
- Manage Flow: Monitor and optimize the flow of tasks.
- Feedback Loops: Conduct regular reviews and retrospectives.
- Continuous Improvement: Iterate and refine the process.
Advantages and Disadvantages of Kanban:
How the Kanban strategy is helpful:
Kanban enables real-time collaboration, ensuring tasks move seamlessly, reducing lead time, and enhancing productivity.
Learn More: Kanban Training
3. Six Sigma
How is Six Sigma useful for organizations?
Six Sigma aims to improve quality by identifying and removing causes of defects. It helps organizations in ensuring consistent and high-quality output.
Steps to Follow:
- Define: Set goals and customer deliverables.
- Measure: Assess current processes.
- Analyze: Identify root causes of defects.
- Improve: Implement changes to enhance processes.
- Control: Monitor and maintain improved processes.
Advantages and Disadvantages of Six Sigma:
How Six Sigma strategy is helpful:
Six Sigma provides a rigorous methodology for quality assurance, leading to reduced errors, increased customer satisfaction, and substantial cost savings.
Learn more: Design for Six Sigma Training
4. Total Quality Management (TQM)
How is TQM useful for organizations?
TQM is a holistic approach to long-term success through customer satisfaction. It involves all members of an organization in improving processes, products, services, and culture.
Steps to Follow:
- Customer Focus: Prioritize customer needs.
- Continuous Improvement: Regularly evaluate and refine processes.
- Employee Involvement: Engage all members in quality improvement.
- Data-Driven Decision Making: Base decisions on data and analysis.
- Strategic Approach: Integrate quality as a core component of business strategy.
Advantages and Disadvantages of TQM:
How the TQM strategy is helpful:
TQM emphasizes a quality culture, ensuring that every aspect of the organization, from processes to people, is aligned toward delivering superior value.
Learn More: Quality Management Training
5. Agile Methodology
How is Agile Methodology useful for organizations?
Agile promotes adaptive planning, early delivery, and continuous improvement. It helps organizations respond quickly to changes, ensuring products/services remain relevant and competitive.
Steps to Follow:
- Product Backlog Creation: List all desired features, changes, and enhancements
- Sprint Planning: Decide on tasks to be done in a short cycle (sprint).
- Daily Stand-ups: Daily short meetings to update on progress.
- Sprint Review: Assess the work done in the sprint.
- Sprint Retrospective: Reflect on the process and plan improvements.
Advantages and Disadvantages of Agile Methodology:
How the Agile Methodology strategy is helpful:
Agile enables organizations to rapidly adapt to market changes, continuously incorporate feedback, and deliver value faster and more efficiently.
Learn More: Agile Team Development Training
Which Continuous Improvement Strategy Works Best?
When choosing a continuous improvement strategy, the best approach often depends on the organization's needs, challenges, and goals.
Before selecting a strategy, clearly understand your organization's primary challenges. Are you looking to improve quality, speed delivery, reduce waste, or better manage work processes? Here is a neutral perspective:
- Six Sigma or Agile Strategies: Using data-driven techniques, Six Sigma standardizes and optimizes processes for consistent quality during scaling, while Agile addresses complexity through iterative development and feedback, enabling real-time adaptation and refinement as organizations grow.
- Kanban or Lean Strategies: Kanban ensures resource availability by visualizing work, limiting work-in-progress, optimizing flow, and reducing overburden. Lean Strategy emphasizes just-in-time production, ensuring resources are available precisely when needed, eliminating waste from overproduction or stockpiling.
- TQM and Agile Strategies: TQM embeds quality into organizational culture by promoting company-wide participation in continuous improvement. Agile fosters a collaborative culture, emphasizing adaptability, customer feedback, and cross-functional team interactions.
- Agile or Six Sigma or TQM Strategies: Agile emphasizes flexibility, allowing teams to adapt rapidly to changes through iterative cycles and feedback loops. In contrast, Six Sigma and TQM provide structured methodologies for systematic process improvements and consistent quality assurance.
Conclusion
Continuous improvement strategies allow organizations to adapt, evolve, and excel. Each method offers unique benefits for different operational contexts, scales, and desired outcomes. Ensuring that your chosen approach aligns with your organization's objectives, resources, and culture is crucial.
Continuous improvement is about implementing a particular methodology/strategy and fostering a constant growth and enhancement culture. While strategies like Lean, Kanban, Six Sigma, TQM, and Agile offer structured frameworks, the most effective approach often emerges from a tailored combination based on specific needs. Edstellar stands as a one-stop solution for all organizational training needs, ensuring that businesses can effectively integrate and realize the full potential of their chosen continuous improvement strategy.
Explore High-impact instructor-led training for your teams.
#On-site #Virtual #GroupTraining #Customized
Edstellar Training Catalog
Explore 2000+ industry ready instructor-led training programs.
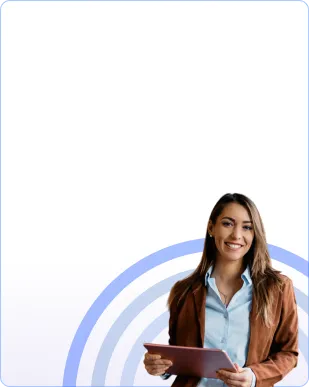
Coaching that Unlocks Potential
Create dynamic leaders and cohesive teams. Learn more now!
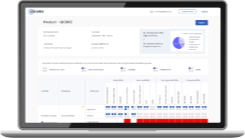
Want to evaluate your team’s skill gaps?
Do a quick Skill gap analysis with Edstellar’s Free Skill Matrix tool
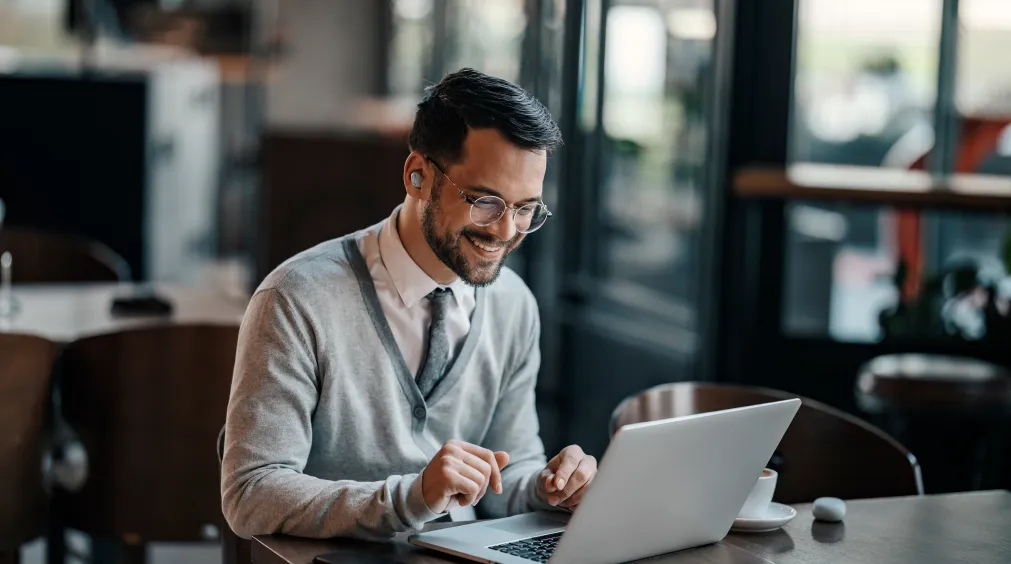
Transform Your L&D Strategy Today
Unlock premium resources, tools, and frameworks designed for HR and learning professionals. Our L&D Hub gives you everything needed to elevate your organization's training approach.
Access L&D Hub Resources